Common Precision Issues in Vertical lathe machine and Solutions
In the context of increasingly fierce competition in modern manufacturing, the vertical lathe machine, as a core machine for processing large workpieces, is widely used in industries such as aerospace, automotive manufacturing, and energy. As technology continues to advance, the precision requirements for vertical lathe machines are growing higher, and precision issues have become a critical factor affecting production efficiency and product quality.
Although vertical lathe machines' high load-bearing capacity and excellent machining performance make them essential in many complex machining tasks, precision fluctuations, machining errors, and other issues still frequently occur during actual operation. In severe cases, these issues can halt the entire production line, resulting in increased costs for enterprises.
Therefore, in-depth analysis of common precision issues in vertical lathe machine machining and proposing corresponding solutions has become crucial for improving manufacturing quality and enhancing market competitiveness. Let's explore how to solve these issues.
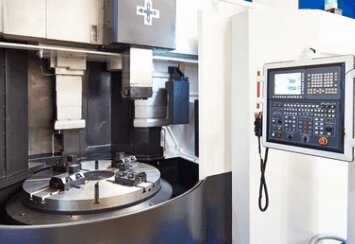
I. Common Precision Issues
Vibration
Vibration is one of the main causes of increased surface roughness and dimensional deviations in machining. It manifests in various forms, such as periodic vibrations caused by spindle system imbalance or non-periodic shocks caused by improper tool installation. Other factors, such as insufficient or uneven workpiece clamping force and unstable machine foundations, can also induce varying degrees of vibration. Research shows that when the amplitude exceeds a certain threshold, the machining quality will significantly degrade.
Thermal Deformation
During the operation of the cnc vertical lathe machine, heat is inevitably generated, causing various components of the machine tool to expand and deform to varying degrees. For example, axial elongation of the spindle box due to heat may lead to workpiece cylindricality errors, while thermal expansion of the guideways can affect linear motion accuracy.
Geometrical Errors
Geometrical errors mainly include guideway straightness errors, spindle rotation errors, and worktable flatness errors. These errors directly determine the shape and positional accuracy of the workpiece. Any slight deviation may result in the final product not meeting design specifications.
Material Properties
Different materials have different physical properties, such as hardness, ductility, and thermal conductivity. These properties not only affect the force distribution during the cutting process but also significantly influence the final product's accuracy. For instance, in the case of hard alloys, higher hardness helps maintain the sharpness of the cutting edge but also increases cutting resistance, making vibration more likely.
Operational Errors
In addition to the above objective factors, the technical skill of operators cannot be overlooked. Errors such as incorrect parameter settings and untimely tool changes can have a negative impact on the results. Especially in multi-process composite machining, any deviation in one link can lead to the failure of the entire machining process.
II. Five Solutions
Optimize Structural Design to Reduce Vibration
· Select High-Performance Dampers: For different vibration frequency ranges, selecting a damper with an appropriate damping ratio can significantly reduce interference from the external environment.
Vibration Frequency Range | Suitable Damper Type | Selection Reason |
1 - 10 Hz (Low Frequency) | Metal Spring Damper | Uses spring elasticity to buffer vibrations; reasonable damping design can prevent resonance. Damping ratio: 0.05 - 0.2. |
Above 10 Hz (High Frequency) | Rubber Damper | Has good high-frequency vibration isolation properties; elastic and damping properties quickly dissipate high-frequency vibrations. Damping ratio: 0.2 - 0.5. |
· Precise Balance Adjustment: Perform comprehensive inspection of the vertical lathe machine's spindle system and make precise balance adjustments based on measurement results to ensure smooth operation with no noise.
· Improved Clamping Method: Use flexible fixtures or hydraulic chucks instead of traditional rigid clamping to ensure adequate rigidity and stability while avoiding deformation caused by excessive clamping force.
· Reinforce Foundation: Regularly check and maintain the machine's foundation bolts and other connectors to ensure that the machine is securely installed and reliable.
Control Temperature Changes to Prevent Thermal Deformation
· Optimize Cooling System Configuration: Choose high-performance cooling pumps and large-flow nozzles to ensure the cutting fluid sufficiently covers areas that need cooling.
· Maintain Suitable Workshop Temperature: Install precision air conditioning systems in the workshop to strictly control the room temperature within an appropriate range.
· Reasonable Production Scheduling: Avoid prolonged continuous operation of the same machine and allow it enough time to rest and dissipate heat.
Regular Calibration to Ensure Geometrical Accuracy
· Introduce Advanced Detection Methods: Use high-precision instruments such as laser interferometers and coordinate measuring machines (CMM) to regularly check parameters like guideway straightness.
· Timely Repair of Worn Parts: Based on detection results, promptly correct deviations and replace heavily worn components when necessary.
· Establish Quality Management System: Implement a comprehensive quality management system, standardize daily maintenance processes, and prevent potential issues from arising.
Reasonable Material and Process Selection
· Scientific Material Selection: According to the ISO 513-1975 standard, different types of hard alloys have different application areas. Selecting the correct material can significantly improve machining efficiency and accuracy.
Workpiece Material | Material Properties | Recommended Tool Materials | Tool Material Advantages |
Hard Alloys | High hardness, good wear resistance, but high cutting resistance and prone to vibration | Carbide tools, CBN tools, PCD tools | High hardness, wear resistance, suitable for high-temperature cutting, stable processing of hard alloys |
Aluminum Alloys | Lightweight, good ductility, good cutting performance | HSS tools, Coated carbide tools | Low cutting force, suitable for high-precision machining, extends tool life |
Stainless Steel | High hardness, poor cutting performance, prone to heat buildup | Coated carbide tools, ceramic tools | Heat-resistant, wear-resistant, improves machining precision and surface quality |
Titanium Alloys | High strength, excellent corrosion resistance, but poor cutting performance and high cutting temperature | Coated carbide tools, CBN tools | Heat-resistant, wear-resistant, stable cutting, extends tool life |
Copper Alloys | Good ductility, low hardness, easy to machine, good thermal conductivity | HSS tools, carbide tools | Low cutting force, good surface quality, suitable for high-precision machining |
Plastics | Easy to cut, but may cause melting during machining | Carbide tools, PCD tools | Efficient cutting, prevents melting, maintains good surface quality |
Strengthen Personnel Training
· Professional Skill Training: Regularly arrange training for operators with experts or experienced technicians. The training should cover machine structure, cutting principles, tools, and programming knowledge, helping operators master the applicable tools and cutting parameters.
· Create Detailed Operation Manuals: Develop clear and illustrated operation manuals based on the characteristics of the cnc vertical lathe machine and machining processes. The manuals should include recommended parameters and adjustment methods for different materials and tools in the form of charts.
· Error-Proofing Devices: Install error-proofing sensors in key areas like tool and workpiece clamping. If an error occurs, the machine will immediately alert the operator and stop the machine, preventing precision issues and equipment damage.
By implementing the above measures, not only can precision issues in vertical lathe machine machining be effectively resolved, but machining efficiency and product quality can also be further enhanced, creating greater value for the enterprise. If you have further questions about solving precision issues in vertical machining or are looking for a suitable vertical lathe machine, feel free to visit our official website for free consultation!