How Does CNC Milling and CNC Drilling Compare?
It’s just a hole—does it really matter whether you drill it or mill it?
The key difference between CNC drilling and CNC milling is that drilling focuses on efficient creation of standard holes, while milling is better suited for complex geometries, contours, grooves, and multi-step operations.
Next, we’ll look at real-world applications to help you clearly understand the differences and choose the right machining process for your parts.
1. CNC Milling vs CNC Drilling: Which One to Choose?
1.1 What is CNC Drilling
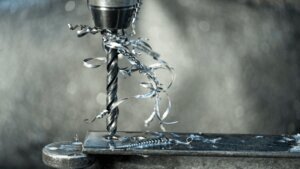
CNC Drilling is a process where a rotating drill bit moves along the Z-axis to create straight, cylindrical holes into a workpiece. It's designed for high-speed, high-precision hole-making, especially in repetitive or high-volume scenarios.
Process type: Point cutting
Tool movement: Z-axis vertical feed
Common tools: Twist drills, step drills, center drills, deep hole drills
Typical hole tolerance: ±0.05 mm
Best suited for: Standard holes, high-volume, multi-hole operations
CNC drilling is ideal for workpieces that require fast, consistent hole creation—such as cooling plates, mounting holes, fastener bores, and PCB layouts.
1.2 What is CNC Milling?
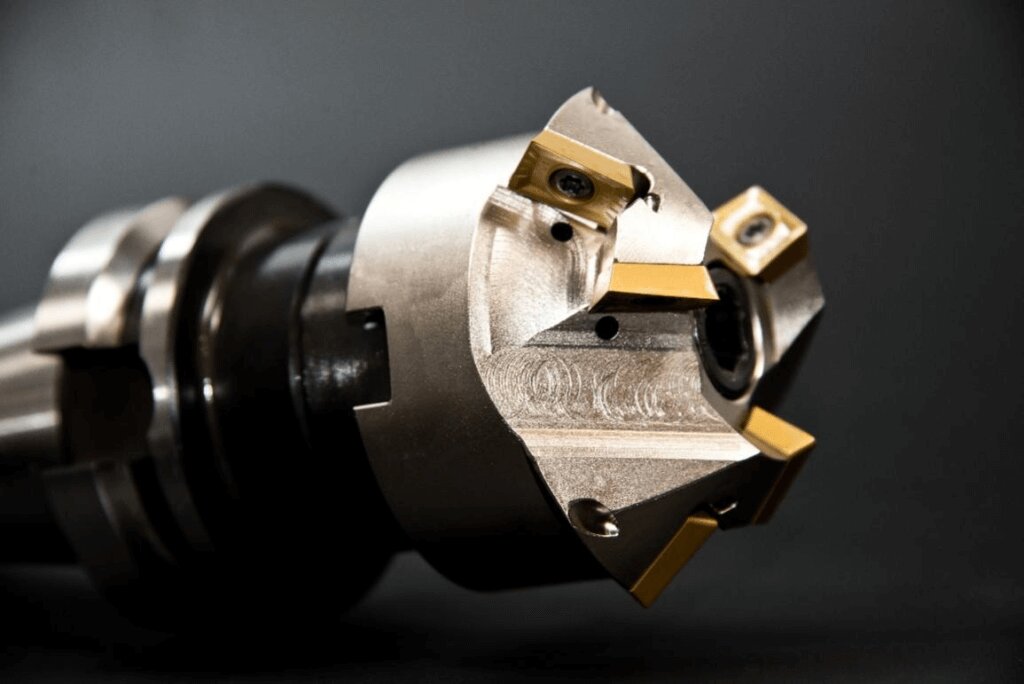
CNC Milling involves rotating cutting tools that move along multiple axes (X, Y, Z, or more) to remove material. Unlike drilling, milling can perform complex machining—such as flat surfaces, contours, cavities, and custom shapes—all in a single setup.
Process type: Surface and contour cutting, multi-axis
Tool movement: Typically X/Y/Z, optionally 4- or 5-axis simultaneous control
Common tools: End mills, ball nose mills, face mills, slot mills
Best for: Flat surfaces, pockets, grooves, contours, multi-feature parts
Typical applications: Mold cavities, aerospace brackets, medical parts, housings
CNC milling is best when your parts have complex geometry, require multiple cutting operations, or need a high-quality surface finish.
1.3 Typical Use Cases: When to Use CNC Milling or CNC Drilling?
✅ CNC Milling is ideal for:
Complex contours and structural components
Used in aerospace, medical implants, or engine parts where precise 3D geometry is required.
Surface machining and multi-step grooves
Perfect for machine bases, guides, T-slots, and stepped features, all done in a single setup.
Multi-process hybrid operations
Milling machines with automatic tool changers can perform drilling, tapping, chamfering, and contouring all in one cycle.
✅ CNC Drilling is ideal for:
High-density hole arrays
Used in heat sinks, flanges, valve plates, or control panels with many repeated hole patterns.
Mounting holes and precision dowel locations
Essential for jigs, fixtures, or assemblies requiring precise fits.
Deep holes and step bores
When used with long drills and high-pressure coolant systems for deep and clean holes.
High-volume standard hole production
Great for parts like support brackets, chassis plates, or electrical enclosures where speed and consistency matter.
1.4 Comparison Table: CNC Milling vs CNC Drilling
Aspect | CNC Milling | CNC Drilling |
Tool movement | Multi-axis (X/Y/Z or more) | Single-axis (Z-axis only) |
Cutting capability | Surfaces, grooves, profiles, pockets | Round holes only (including step & deep) |
Common tooling | End mills, ball mills, face mills | Twist drills, center drills, gun drills |
Accuracy | High (up to ±0.01 mm) | Medium to high (around ±0.05 mm) |
Machine configuration | Multi-axis machining centers | Drill presses or converted machining centers |
Best use cases | Custom parts, low to medium volume, complex shapes | High-volume, standard hole production |
Cutting speed | Moderate, slower for high precision | Very fast for simple hole drilling |
Equipment cost | Higher investment for multi-function use | Lower initial investment |
Programming complexity | High, requires CAM expertise | Low, template-based programming |
Flexibility | High, good for job shops and prototyping | Low, for fixed and repetitive tasks |
2. Advantages and Disadvantages of CNC Milling and Drilling
2.1 Pros and Cons of CNC Milling
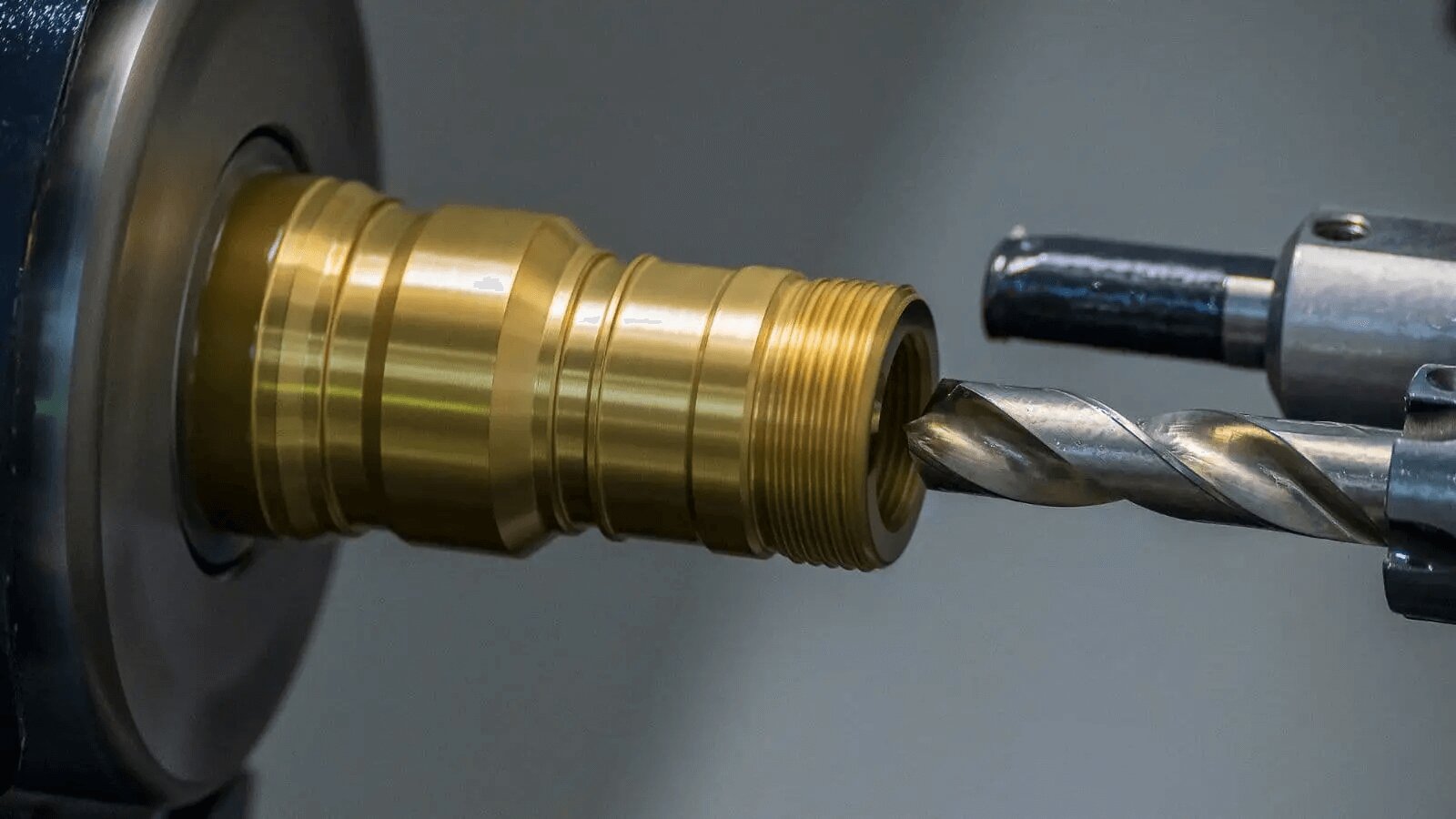
Milling is ideal for versatility and complex geometry. Benefits include:
•Capable of machining complex profiles, cavities, and 3D surfaces
•Can perform multiple operations in one setup
•Higher dimensional accuracy and better repeatability
•Great for custom, low-volume, or precision parts
•Controlled paths deliver better surface finish and consistency
Limitations of CNC Milling include:
•Slower than drilling for simple hole-making
•Higher machine and tooling costs
•Requires skilled programmers and operators
•Higher energy usage and cooling requirements
•Less efficient for hole-only production
2.2 Pros and Cons of CNC Drilling
Drilling is simple, fast, and efficient for hole-making. Key advantages:
•Fastest method for creating cylindrical holes
•Machines are more affordable
•Lower energy consumption
•Easy to install, use, and maintain
•Ideal for repetitive and high-volume tasks
•Simple programming with minimal training required
However, drilling has its limitations:
•Not suitable for non-cylindrical features or surface machining
•Lower geometric flexibility compared to milling
•Typically produces rougher surface finishes
•Not ideal for material removal over large areas
•Limited to vertical hole creation only
•Cannot handle angled paths or complex part shapes
3. Conclusion: CNC Milling or Drilling? Let Us Help You Choose
Each machining method has its strengths:
Choose CNC milling when your parts require complex shapes, contours, or multi-step machining.
Choose CNC drilling when you're producing many standard holes and speed is the priority.
Can’t decide? Go with a hybrid solution—many modern machining centers can mill and drill in one setup.
As a machine tool manufacturer and CNC solution provider, we don’t just sell equipment—we help you choose the right one.
Not sure which to use? Let us help.
Send us your part drawings or machining requirements. The Minnuo engineering team will analyze your needs and recommend the most cost-effective, efficient machining process and equipment setup for your production.
✅ Optional FAQ Section
Q: What kind of parts is CNC drilling best for?
A: Drilling is best for panels, brackets, flanges, or any part requiring consistent, high-volume hole making.
Q: Is CNC milling worth the higher investment?
A: Yes, if your parts involve complex features, high precision, or multi-operation workflows, milling provides greater value over time.
Q: Can one machine do both drilling and milling?
A: Absolutely. Many modern CNC machining centers can switch tools automatically to handle both processes in a single setup.