How many axes does a manual lathe have?
How many axes does a manual lathe have?
In a world increasingly dominated by automation and high-tech innovations, there’s a growing appreciation for traditional, hands-on tools. While CNC machines boast impressive precision and speed, manual lathes continue to hold their own in workshops and educational institutions. The charm of mastering a manual lathe lies not only in its simplicity but also in the artistry and skill required to produce precise components. This brings us to a common question: how many axes does a manual lathe have, and how does this impact its operations?
At its core, a manual lathe operates with two primary axes: the X-axis for radial movements and the Z-axis for longitudinal movements. These axes form the foundation for essential operations such as turning, facing, threading, and grooving. Some advanced manual lathes or attachments even introduce additional axes, expanding their capabilities for more complex tasks. Understanding these axes is key to unlocking the full potential of manual machining.
In this article, we’ll explore the roles of these axes, the benefits and limitations of manual lathes, and how to choose the right machine for your needs. Whether you’re a seasoned machinist or a beginner, this guide will provide practical insights to help you make the most of this versatile tool.
Understanding the Axes on a Manual Lathe
Definition of Axes in Machining Context
In machining, an "axis" refers to a direction of movement that a tool or workpiece can traverse or rotate to execute specific machining tasks. Each axis represents a degree of freedom, and the ability to control movement along these axes determines the complexity and versatility of the machine.
For manual lathes, the focus is primarily on linear axes. Unlike CNC lathes that operate with automated precision across multiple axes, manual lathes rely on the operator to control the tool and carriage movements manually. Despite their simplicity, understanding these axes is essential for performing accurate operations such as turning, facing, and threading.
Primary Axes on a Manual Lathe
Manual lathes typically feature two main axes, which provide the fundamental directions of movement necessary for machining:
X-Axis (Radial Movement)
The X-axis controls the tool's movement perpendicular to the workpiece’s axis of rotation. This movement is often referred to as the radial direction and is crucial for:
1. Facing Operations: Creating flat surfaces on the end of the workpiece.
2. Profiling: Shaping specific contours or cutting grooves across the radius of the material.
Operators achieve this movement by manipulating the cross slide, which is mounted on the carriage and supports the tool post. The precision of X-axis control determines the smoothness and accuracy of the surface finish.
Z-Axis (Longitudinal Movement)
The Z-axis controls the carriage's movement parallel to the workpiece’s axis of rotation. This is known as longitudinal movement and is essential for:
1. Turning Operations: Reducing the diameter of a workpiece along its length.
2. Threading and Grooving: Creating threads or grooves that follow the length of the material.
This movement is guided by the carriage, which travels along the bed of the lathe. Combined with the rotation of the spindle, the Z-axis enables operations like cylindrical turning with consistent dimensions.
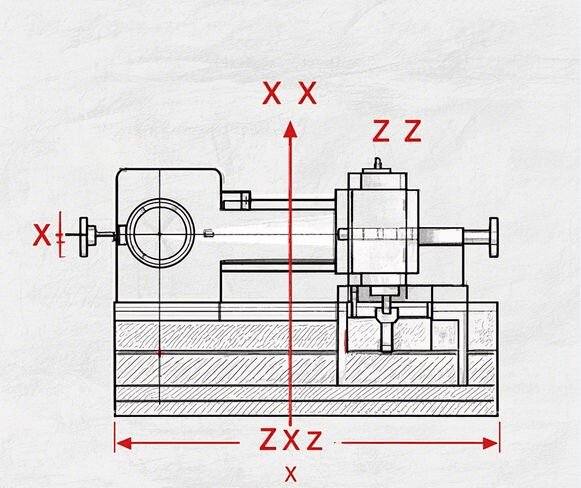
Optional Axes on Certain Models
While standard manual lathes are limited to the X and Z axes, some advanced manual lathe models or specialized attachments may incorporate additional axes:
Rotational Axes:
Some lathes allow the tool or workpiece to rotate around a secondary axis, providing additional flexibility for complex geometries. For example, a tool post with a swiveling base can facilitate angled cuts without repositioning the workpiece.
Manual or Compound Slide Axes:
The compound slide offers a manually adjustable third axis, often set at an angle, enabling the operator to perform taper turning or other specialized cuts. This adds a degree of versatility to the machine while retaining manual control.
These optional axes expand the range of operations that can be performed on a manual lathe, making them more adaptable to varied machining tasks.
Difference Between Manual and CNC Lathes in Axis Count
The distinction between manual and CNC lathes is stark when it comes to the number of axes and their functionality:
Manual Lathe Simplicity:
1. Two Primary Axes: The X and Z axes on manual lathes are straightforward and rely entirely on operator skill.
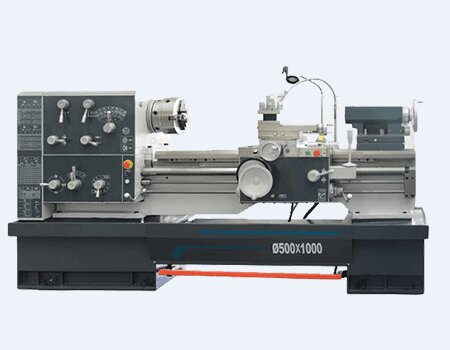
2. Manual Control: Movements are controlled by handwheels, levers, and dials, requiring precision and expertise from the machinist.
3. Limited Automation: While some models may have power feeds, the overall operation demands continuous human oversight.
CNC Lathe Complexity:
1. Multiple Axes: CNC lathes often feature 3 to 5 axes or more, including additional linear (Y-axis) and rotational (A, B, C) axes. This allows for intricate operations like off-center drilling, milling, or simultaneous multi-face machining.
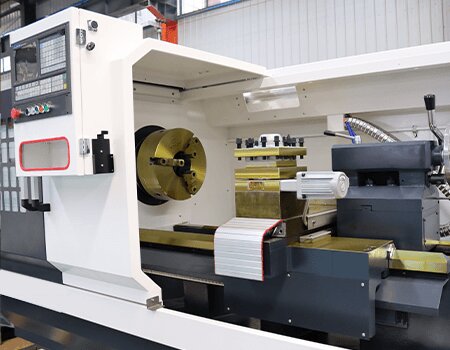
2. Automated Movements: Programmed via Computer Numerical Control, CNC machines execute pre-designed routines with high precision and repeatability.
3. Increased Efficiency: The added axes and automated controls enable faster production, especially for complex parts.
While CNC lathes offer significant advantages in automation and capability, manual lathes remain an invaluable tool for straightforward operations, cost-sensitive projects, and training purposes.
Role of Each Axis in Manual Lathe Operations
X-Axis Operations
The X-axis on a manual lathe enables movement of the cutting tool in the radial direction, perpendicular to the workpiece’s rotational axis. This axis is crucial for machining operations that modify the diameter or surface profile of the workpiece. Key operations include:
Facing Operations
Facing involves moving the cutting tool along the X-axis to create a smooth, flat surface on the end of the workpiece. This operation is commonly performed to square off the ends of cylindrical stock or prepare a surface for subsequent machining. Precision control along the X-axis ensures a uniformly flat face and high-quality finish.
Profile Turning
In profile turning, the cutting tool follows a predefined radial path to create specific contours or features on the workpiece, such as grooves, tapers, or rounded edges. This operation often requires skillful manipulation of the X-axis handwheel to achieve the desired shape while maintaining dimensional accuracy.
By mastering X-axis movements, machinists can produce components with consistent and precise radial features.
Z-Axis Operations
The Z-axis allows the cutting tool to move longitudinally, parallel to the workpiece’s axis of rotation. This motion is fundamental for shaping the overall length and profile of the workpiece. Common Z-axis operations include:
Longitudinal Turning
Longitudinal turning involves feeding the cutting tool along the Z-axis to remove material from the surface of the workpiece, reducing its diameter to create a cylindrical shape. This is one of the most basic and essential operations on a manual lathe, used to produce shafts, rods, and other symmetrical components.
Grooving and Threadin
1. Grooving: The tool moves along the Z-axis to create narrow channels or cuts of specific depths and widths on the workpiece. This operation is often used for applications such as retaining rings or decorative features.
2. Threading: In threading, the cutting tool follows the Z-axis while the spindle rotates at a precise rate to produce helical grooves (threads). Proper synchronization between the tool’s feed rate and the spindle speed is critical to ensure accurate thread geometry.
The Z-axis plays a central role in operations requiring uniformity along the length of the workpiece, making it indispensable for machining cylindrical parts.
Coordination Between Axes
The true versatility of a manual lathe lies in the coordination of the X and Z axes, which allows machinists to perform complex and precise machining tasks.
Importance of Synchronized Movements
Coordinating movements along both axes enables the creation of intricate geometries, such as tapers, chamfers, and curves. For example:
1. Taper Turning: By simultaneously advancing the tool along both axes, machinists can produce gradual changes in diameter, creating a tapered profile.
2. Filleting and Rounding: Controlled blending of X and Z axis movements produces smooth transitions between surfaces, enhancing the aesthetic and functional qualities of the workpiece.
Examples of Typical Machining Tasks
1. Complex Profiles: Shaping components like pulleys or flanges often requires precise coordination of the X and Z axes to ensure accurate dimensions and consistent finishes.
2. Custom Features: Creating unique parts for prototypes or small-batch production frequently involves combining facing, turning, and grooving operations across both axes.
By mastering the coordination between the X and Z axes, machinists can unlock the full potential of a manual lathe, achieving both high precision and versatility in their machining processes.
Benefits and Limitations of Manual Lathes with Two Axes
Benefits of Manual Lathes with Two Axes
Manual lathes with two axes (X and Z) offer a range of benefits that make them a preferred choice for certain applications:
Simplicity and Accessibility
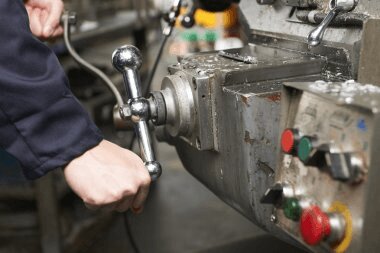
1. Ease of Operation: The straightforward design of manual lathes makes them easy to learn and operate, making them ideal for beginners or those with limited machining experience.
2. Minimal Maintenance: With fewer components and no complex electronics, manual lathes require less upkeep compared to CNC machines, reducing downtime and maintenance costs.
Cost-Effectiveness
1. Lower Initial Investment: Manual lathes are more affordable than CNC counterparts, making them a practical option for small workshops, hobbyists, and educational institutions.
2. Operational Savings: Since manual lathes don’t rely on advanced technology, they eliminate the need for expensive software or control systems, further lowering operational costs.
Versatility in Simple Tasks
1. Custom and One-Off Jobs: Manual lathes excel in producing custom parts or handling one-off projects where programming a CNC machine would be inefficient.
2. Quick Adjustments: The manual nature of the machine allows operators to make real-time adjustments, providing flexibility during machining.
Ideal for Training and Skill Development
1. Manual lathes serve as an excellent platform for learning the fundamentals of machining, such as tool selection, cutting speeds, and feed rates.
2. These machines cultivate hands-on skills, which are critical for troubleshooting and understanding advanced automated systems.
Limitations of Manual Lathes with Two Axes
While manual lathes are invaluable for certain tasks, their two-axis design imposes some limitations:
Restricted Functionality
1. Limited Axial Movement: With only two linear axes, manual lathes cannot perform operations requiring multi-directional movement, such as complex contouring or off-center machining.
2. Inability to Handle Complex Parts: Producing parts with intricate geometries or multiple features requires advanced setups or specialized attachments, which increases time and effort.
Operator Dependency

1. Skill-Intensive: The quality of the finished product heavily depends on the operator’s expertise, leaving room for human error.
2. Inconsistent Results: Achieving uniformity across multiple parts is challenging without advanced skills and experience.
Slower Production Rates
1. Manual Control Limits Speed: Unlike CNC lathes that can execute pre-programmed operations rapidly, manual lathes rely entirely on the operator, resulting in slower cycle times.
2. Reduced Efficiency in High-Volume Production: For large-scale manufacturing, manual lathes are inefficient compared to automated systems.
Lack of Advanced Capabilities
1. No Automation: Manual lathes cannot perform automated processes, such as repetitive cycles or multi-axis coordination, which are essential for modern precision machining.
2. Limited Integration: They cannot be easily integrated into automated production lines, reducing their compatibility with modern manufacturing environments.
Balancing the Benefits and Limitations
Despite their limitations, manual lathes remain an essential tool in many machining contexts. By understanding their strengths and weaknesses, operators can leverage these machines for tasks where their benefits outweigh their drawbacks. For example:
· Best Use Cases: Manual lathes are ideal for repair work, prototyping, or small-batch production where flexibility and hands-on control are more important than speed.
· Enhancements: Adding features like a Digital Readout (DRO) system can improve accuracy and efficiency, helping to mitigate some limitations.
· Complementary Role: In a workshop with CNC machines, manual lathes serve as a cost-effective backup or as a training tool for new operators.
How to Choose a Manual Lathe Based on Axis Count
Factors to Consider
Selecting the right manual lathe based on axis count involves evaluating your specific machining needs and constraints. Here are the key factors to consider:
Type of Work
1. Simple Turning Tasks:
If your primary focus is on straightforward operations such as cylindrical turning, facing, or threading, a standard two-axis manual lathe is sufficient. It handles basic machining tasks efficiently and offers the simplicity needed for routine work.
2. Complex Shapes:
For projects requiring angled cuts, tapers, or intricate contours, consider a lathe equipped with a compound slide or other enhancements that provide additional axes or angular adjustability. This adds versatility, enabling you to handle a wider range of tasks.
Budget
1. Manual lathes are generally more affordable than CNC machines, but additional features like compound slides or digital readout (DRO) systems increase the cost. Determine how much you're willing to invest based on the scope of your machining needs and how much value the added functionality will provide.
Workshop Space Constraints
1. Manual lathes come in various sizes. A compact bench lathe is suitable for hobbyists or small workshops with limited space. For larger or industrial-scale operations, a floor-mounted lathe may be more appropriate, provided you have adequate room and infrastructure.
Practical Tips
To make the most informed decision when choosing a manual lathe, follow these practical guidelines:
Start with a Standard Two-Axis Manual Lathe
1. If you’re new to machining or your projects primarily involve basic turning and facing operations, a two-axis manual lathe is the best starting point. It’s straightforward to use, cost-effective, and perfect for learning machining fundamentals.
2. Standard two-axis lathes are versatile enough to cover most general-purpose machining needs, especially for small-scale or custom work.
Consider Upgrades for Added Functionality
1. Tool Attachments: Invest in tool post attachments such as knurling tools, boring bars, or specialized cutting tools to expand your machining capabilities without changing the machine's core design.
2. Compound Slide: If your work often involves taper turning or angular cuts, a lathe with a compound slide can provide more control and flexibility.
3. DRO Systems (Digital Readout): Installing a DRO system significantly enhances accuracy by providing real-time feedback on tool position. This is particularly useful for tasks requiring tight tolerances or repeatability.
4. Power Feed: Adding a power feed to one or both axes can improve efficiency and reduce operator fatigue during long or repetitive cuts.
Plan for the Future
1. Think ahead about the types of projects you aim to undertake. While a basic lathe may suffice initially, ensure your chosen model can be upgraded or adapted to meet evolving requirements.
Conclusion
Manual lathes are essential for machining, combining simplicity, reliability, and precision for a variety of tasks. A standard two-axis model is an excellent starting point for most users, with upgrade options available to meet evolving needs. With thoughtful planning and the right machine, a manual lathe can be a valuable long-term asset.
If you’re searching for the ideal manual lathe, visit MINNUO website for free consultations and explore our range of high-quality manual machine tools.