Advantages and Disadvantages of Lathes
With the continuous advancement of intelligent manufacturing, companies are faced with increasingly diverse options when selecting machining equipment. Lathes, milling machines, machining centers, and turn-mill machines... all seem capable of “machining,” but their performance differs greatly, and each requires a different level of investment. Among so many types of equipment, is the lathe still worth having a place?
Although lathes offer advantages such as high efficiency, mature technology, and easy maintenance, they also have limitations such as a restricted machining range and single functionality. Therefore, when selecting a lathe, one must evaluate it carefully based on product structure and production line needs.
This article will break down the structure, classifications, advantages, and disadvantages of lathes, and provide clear selection advice based on practical scenarios to help you determine whether a lathe truly suits your production needs.
I. What Is a Lathe? From Principles to Evolution and Classification
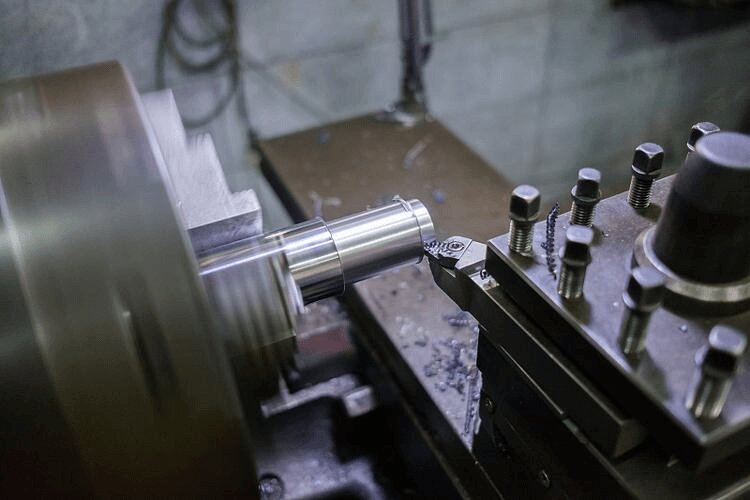
1️⃣ Working Principle:
A lathe is a machine tool that allows the workpiece to rotate at high speed while the cutting tool is either fixed or programmed to move for machining. Its core feature is: "the workpiece moves, while the tool remains stationary" or "the workpiece moves, and the tool moves under control." This setup is particularly suited for machining symmetrical parts such as outer diameters, end faces, inner holes, threads, and tapers.
2️⃣ Historical Evolution: From Hand-Powered Belts to Smart CNC Lathes
Ancient Times: The Egyptians invented the original wooden lathe powered by human effort.
18th Century: During the Industrial Revolution, modern lathe prototypes emerged, using belt transmission.
1950s: CNC (Computer Numerical Control) technology was introduced, leading to CNC lathes.
Modern Era: Integration with servo control, tool magazine systems, automatic feeding, and vision inspection has enabled highly flexible turn-mill systems.
3️⃣ Classification Overview: By Structure, Control, and Function
Type | Control & Structural Features | Typical Applications |
Manual Lathe | Manually operated, simple structure | Teaching, small batch basic machining |
CNC Lathe | Program-controlled, high repeat accuracy | Precision parts, medium-volume production |
Vertical Lathe | Vertically mounted workpiece, high load capacity | Large disc-shaped parts |
Multi-tool turret, automatic tool change | Medium-to-small parts, high batch machining | |
Turn-Mill Machine | Integrated turning and milling, multi-axis linkage | Complex multi-face parts, one-time setup |
II. Main Components of a Lathe
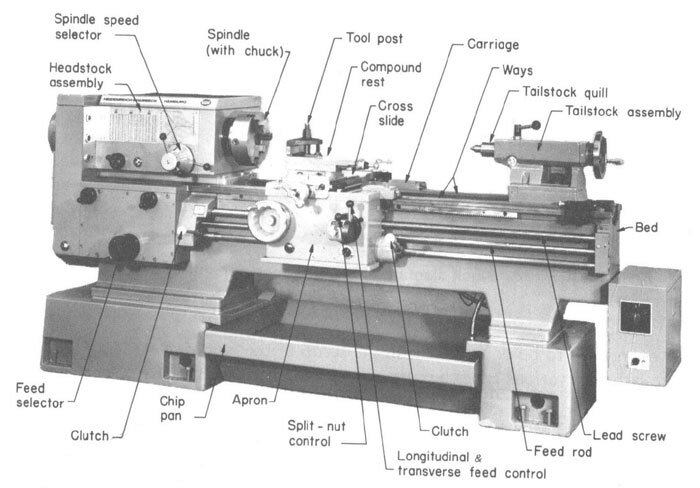
Bed
The bed is the backbone of the lathe, determining its rigidity and stability. Higher rigidity means better performance during heavy cutting.
Headstock
Drives the workpiece to rotate and affects machining accuracy and efficiency. Pay attention to speed range and transmission method.
Chuck
Used to clamp the workpiece. Three-jaw chucks are suitable for standard parts, four-jaw for irregular parts, and hydraulic chucks offer higher automation efficiency.
Tailstock
Supports long workpieces or holds drills, improving machining stability.
Tool Post
Holds the cutting tools. CNC lathes are often equipped with powered turrets, enabling automatic tool changes and multi-process machining.
Carriage and Feed System
Controls tool movement and is key to precise cutting.
III. Advantages and Disadvantages of Lathes
✅ Advantages: The Master of Efficiency, Stability, and Cost Balance
High Cutting Efficiency
Lathes can quickly machine standardized, repetitive parts such as shafts, threads, and sleeves. When paired with automatic feeding, they can achieve lightweight automation.
Mature Structure, Easy Maintenance
After over a century of development, lathe structures and parts are highly standardized, easy to repair, and logical to operate. Maintenance is much simpler than with machining centers.
High Compatibility, Ideal for Shaft Parts
In high-precision rotating parts such as motor shafts or rollers, lathes are nearly irreplaceable.
Low Learning Curve, Skill Transferable
Compared to complex equipment like five-axis machines, lathes are easier to operate and train on, helping reduce labor entry barriers.
High Expandability
Can be equipped with powered turrets, sub-spindles, and Y-axes, enabling advanced machining and light-duty turn-mill capabilities.
❌ Disadvantages:
Only Suitable for “Rotational” Machining
Lathes struggle with asymmetrical, flat, or polygonal workpieces and cannot handle complex 3D parts entirely.
Cumbersome Setup and Re-clamping
Unlike machining centers with automatic tool changers, lathes are less flexible during tool or part changeovers, interrupting the process flow.
CNC Programming Is More Complex Than Manual Operation
Though basic operation is simple, CNC programming requires solid understanding of coordinates and logic—demanding experienced personnel.
Machining Precision Affected by Tool Wear
During long-time continuous operations, worn tools will impact surface quality and need regular replacement and calibration.
IV. Comparison of Lathes and Other Machines
Comparison Metric | Lathe | Milling Machine | Machining Center |
Workpiece Type | Shafts, cylinders, threads | Flats, slots, cavities | Complex 3D parts |
Operation Method | Workpiece rotates, tool moves | Workpiece fixed, tool rotates | Multi-axis tool movement |
Cost | Low to Medium | Medium | High |
Production Line Integration | Core for shaft batch lines | Mold/plate machining | Multi-function composite line core |
Automation Level | Medium (expandable) | Medium (can be linked) | High (ATC, APC modules) |
✅ Selection Tips:
If your parts are mainly shafts, sleeves, or threaded components → choose a lathe.
For flat slots or drilling processes → use milling machines or machining centers.
For complex, multi-surface parts needing full machining in one setup → consider turn-mill or 5-axis centers.
V. Practical Applications: Who Can’t Work Without a Lathe?
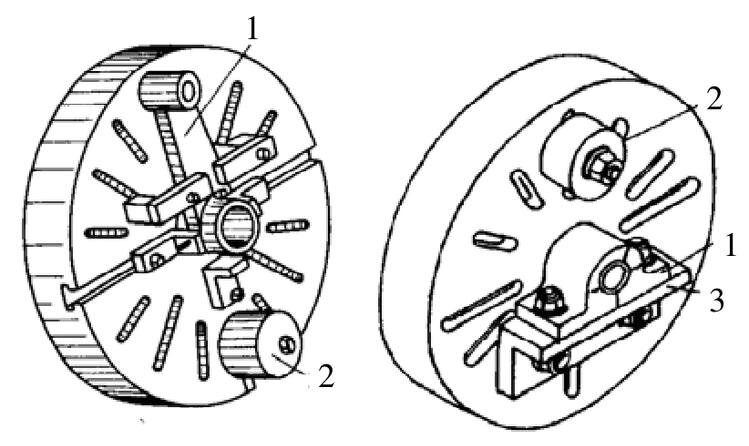
Automotive Parts: Engine shafts, steering rods, transmission sleeves, piston pins
Aerospace: Turbine shafts, connectors, high-temperature alloy cylinders
Railway Industry: Wheel axles, brake nuts, bogie components
Hardware Manufacturing: Standard/non-standard threads, round sleeves
Molds & Fixtures: Guide pillars, guide sleeves, locating shafts
VI. Practical Selection Advice: Who Should Choose a Lathe?
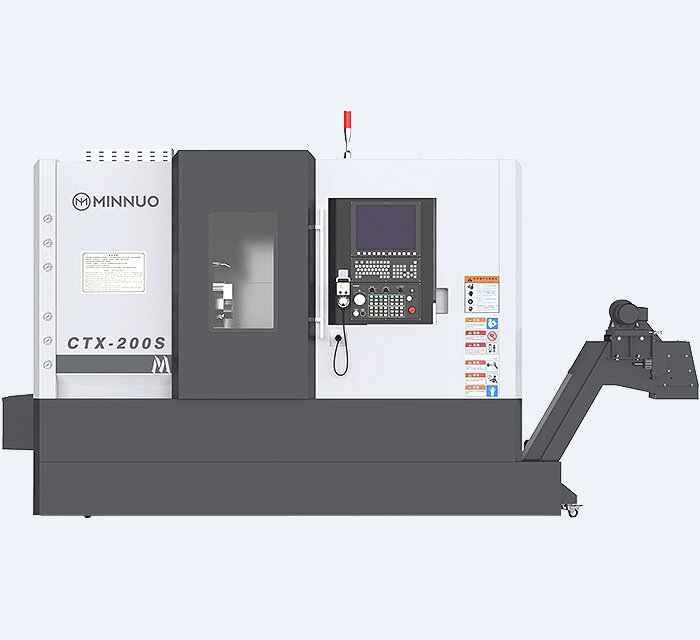
You should consider a lathe if you fall into one of these categories:
Factories producing shafts, threads, sleeves in batches
→ Recommended: CNC lathe + automatic feeder
Small workshops or startups with machining experience but limited budget
→ Recommended: Start with a manual lathe and upgrade later with servo or CNC units
Medium factories needing to complement milling or machining centers
→ Recommended: Combine vertical machining center + CNC lathe to form a flexible line
VII. Conclusion
Machine tool selection is never just about price or specs. It must be based on part geometry, production volume, personnel capability, and future scalability. Especially for shaft-type parts, CNC lathes still offer strong productivity and ROI.
Before making your decision, ask yourself:
Are my products mostly cylindrical or irregular?
Do I have high-volume, repetitive machining needs?
Does my budget support automation?
Can I find suitable operators and programmers?
If you're unsure about any of the above, contact Minnuo. We’ll tailor the right lathe solution for you.