CNC vs. Traditional Machining Compared: Understanding the Differences
In today’s rapidly evolving global manufacturing landscape, businesses are facing diverse production demands. From customized small-batch production to large-scale manufacturing of standardized products, different business scenarios require different machining methods.
CNC (Computer Numerical Control) machining and traditional machining are the two main forces in the manufacturing industry, each demonstrating significant differences in precision control, complex part manufacturing, production efficiency, and data management. These differences are not simply a matter of superiority but reflect their unique suitability for different production contexts.
Let’s take a closer look at the differences between CNC machining and traditional machining in key areas, providing valuable insights for your production decisions.
Ⅰ. Understanding Traditional Machining
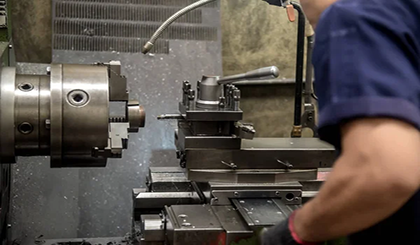
Traditional machining has been the cornerstone of the manufacturing industry for centuries. It encompasses a variety of manual or semi-automated processes. For example, manual milling involves the operator using a milling machine, manually controlling cutting speeds, feed rates, and depths using a handwheel and control levers. This requires significant expertise and deep knowledge of the materials being processed.
Turning on a lathe is another example of traditional machining. The operator mounts the workpiece on a rotating spindle and uses handheld cutting tools to remove material and create cylindrical shapes, threads, and other features. This method demands high skill and experience from the operator, who must understand the material being worked on and adjust cutting parameters to achieve the desired outcome.
Ⅱ. Understanding CNC Machining
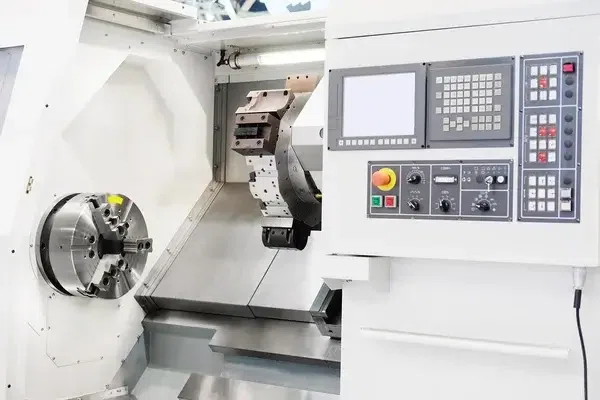
On the other hand, CNC (Computer Numerical Control) machining is a more modern, automated method. It uses pre-programmed computer software to control the movement of the machine tools. For instance, in CNC milling, the operator first creates a 3D model of the desired part using Computer-Aided Design (CAD) software. This model is then converted into G-code that CNC machines can understand.
The CNC machine reads the G-code and precisely controls the movement of cutting tools across multiple axes. This allows for high precision and repeatability. The machine can automatically change tools, adjust cutting speeds, and feed rates, completing complex machining tasks with minimal human intervention.
Ⅲ. Differences Between CNC Machining and Traditional Machining
Comparison Factor | Traditional Machining | CNC Machining |
Precision | Generally, it can achieve an accuracy of ±0.01mm - ±0.05mm. | CNC machines can produce parts with tolerances within the range of ±0.001 inches or even smaller. |
Part Complexity | Difficult to process complex parts. Multiple setups and extensive manual labor are required. | CNC machines can easily process parts with internal cavities, undercuts, and complex curves. |
Production Speed | Small-batch production can be faster in some cases, as there is no need for CNC programming time. | Highly efficient for large-scale production, with the ability to run continuously after programming, greatly reducing overall production time. |
Skill Requirements | High skill level required from operators. They need to manually control the machine, make real-time adjustments, and have in-depth knowledge of machining principles. | Requires skilled operators, but the focus is on programming and machine setup. Proficiency in CAD/CAM software and machining processes is essential, as the machine handles precise cutting operations. |
Ⅳ. Advantages of CNC Machining
High Precision and Repeatability
As mentioned, CNC machining's key advantages are its high precision and repeatability. This ensures that every part produced is identical, which is crucial for industries where quality control is paramount, such as aerospace and automotive.
Improved Production Efficiency
CNC machines can run for extended periods without fatigue. They can perform multiple operations in a single setup, reducing the need for manual handling and repositioning of the workpiece. This increases production efficiency and shortens lead times.
Capability for Complex Part Machining
CNC machining's ability to process complex parts gives it a competitive edge. It enables manufacturers to create innovative designs that were previously impossible, opening up new possibilities for product development.
Reduced Labor Costs
Although CNC machines require an initial investment, they can reduce labor costs in the long run. Since the machines perform most of the precision work, fewer highly-skilled manual operators are needed. Moreover, the reduced production time results in lower overall labor costs per part.
Ⅴ. Advantages of Traditional Machining
Lower Initial Investment
Compared to CNC machines, traditional machining equipment is generally less expensive to purchase. For small-scale manufacturers or businesses with limited budgets, traditional machining may be a more affordable option.
Flexibility for Small-Batch Production
In small-batch production, traditional machining may offer greater flexibility. If a part design changes, adjustments can often be made more quickly and easily in a traditional setup than having to reprogram a CNC machine.
Operator Creativity
Traditional machining allows operators to exercise a degree of creativity. Skilled operators can make on-the-fly adjustments based on intuition and experience to achieve the desired result. This can be especially useful in artistic or custom applications.
Ⅵ. What Advantages Does CNC Technology Have Over Traditional Methods?
· Better Data Management: CNC technology enables easy monitoring and recording of machining processes. This allows for precise collection and analysis of production data, providing strong support for quality control in subsequent steps.
· Enhanced Quality Control and Traceability: With detailed records of the machining process, any quality issues that arise can be quickly traced back to the production phase, pinpointing the root cause and improving quality control efficiency.
· High System Integration: CNC machines can be integrated with larger manufacturing systems, enabling seamless interaction and data exchange with other equipment and software. This enhances the efficiency of production planning and resource allocation, helping businesses improve overall productivity.
Ⅶ. How to Choose Between CNC Machining and Traditional Machining
The choice between CNC and traditional machining depends on several factors. For large-scale production of complex, high-precision parts, CNC machining is the clear choice. Industries such as automotive, aerospace, and electronics rely heavily on CNC machining to produce large quantities of high-quality parts.
On the other hand, traditional machining may be more suitable for small-scale operations, custom products, or situations where initial investment is limited. Hobbyists, small craft manufacturers, and prototype makers may find traditional machining to be easier to implement and more cost-effective.
Ⅷ. Conclusion: The Future of the Machining Industry
Both CNC and traditional machining hold important positions in the manufacturing industry. As technology continues to advance, CNC machining is likely to become more widespread, with improvements in software, automation, and machine performance. However, traditional machining will always have its niche, particularly in fields that place a high value on manual skill and creativity.
When choosing between the two methods, businesses should carefully evaluate their specific needs, production volume, part complexity, and budget. In some cases, combining both CNC and traditional machining could be the most effective approach, leveraging the strengths of both for optimal precision, flexibility, and cost-efficiency.
If you'd like to learn more about manual and CNC machines, feel free to visit MINNUO, where we offer detailed and professional consultations free of charge!